Dean Gehring took the biggest risk of his career when he packed up his bags and moved with his family to Irian Jaya, Indonesia. He had been working in the United States for a copper mining company when he took the opportunity to work an international mine. Gehring was from a small farming community in northern Idaho, never dreaming he would make such a change. Yet, those three years were the eye-opening experience that Gehring carries with him to better understand, develop, and foster a safe, global culture at mineral mining company Rio Tinto Minerals.
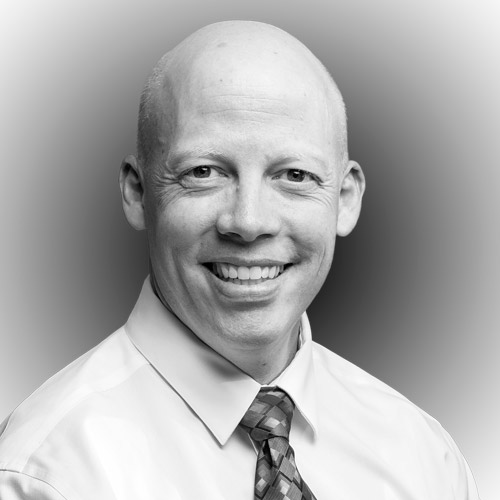
“As I look back on it now, it doesn’t seem like it was a risky career move,” says Gehring, president and chief executive officer at Rio Tinto Minerals. “It was incredibly rewarding just having that opportunity to experience, firsthand, a developing world culture and some of the challenges that came with the extreme operational conditions.”
Now Gehring spends about 25 percent of his time on the road, traveling to a few of the various business-unit sites located in the United States, Europe, and Asia, as well as visiting customers that span more than a hundred countries. When he’s not on the road, Gehring normally gets into the office at 7 a.m., before a majority of the other office workers. Because it’s a global company, this time gives Gehring the opportunity to catch up on e-mails from Asia and Europe that have come in overnight.
The CEO is a big believer in management walking around, so Gehring also ensures he makes time to walk the floor to see how people are doing and get updates of what they may be working on. It gives him the opportunity to do what he calls “microcoaching.” Employees will use that chance to ask questions, and they get insight on how Gehring sees the business. It’s also a major catalyst in forming a collaborative company culture.
Rio Tinto Minerals has a complex structure in that it encompasses everything from mining operations to customer service. The Rio Tinto Minerals team manages the full value stream of operations, supply chain, and customer services, so it’s crucial that the various functions have the authority and autonomy to speak directly to one another.
Even though it is a company of 1,000 employees, Rio Tinto Minerals is very focused on running a lean operation—leaders may have to wear many hats. Employees recognize that they have to have a knowledge and understanding of more than just their area of operation in order to create a truly integrated team.
Gehring believes this holistic view creates a collaborative and transparent work environment that inspires engagement. “Whether it’s using a business system, a process, or piece of equipment, I strongly believe that people come to work wanting to do something meaningful,” Gehring says. “So not only do we look to engage employees through routine business and quality improvement efforts, we also involve employees in special projects. Once you create that space where people can engage in and improve the business, they are more excited about the work they do.”
Another major component that results in multiple generations of employees is Rio Tinto Minerals’ record-low fatality and injury rating. Compared to other industries like construction and forestry, the US Bureau of Labor Statistics lists Rio Tinto Minerals to have a 700 percent lower injury rate per 200,000 hours worked.
In the last twenty-five years that Gehring has worked in the mining industry, he’s seen safety increase dramatically every year. “I constantly tell our employees that there isn’t anything we do that’s worth somebody taking a risk where they can get hurt,” Gehring explains. In 2015 alone, Rio Tinto Minerals completed its safest year in more than one hundred years of the company’s history.
Indeed, Rio Tinto Minerals achieved zero fatalities for the past decade, and last year it listed a rating of one injury for every 600,000 hours of work, which is significantly lower than in previous years. In all but two cases in 2015, the injuries were very minor, allowing the employee to return to work the next day. Gehring is working on continually improving that statistic. “We’re not going to be happy until we have zero fatalities,” he says.
Gehring and his team are putting processes in place to better understand what leads to fatalities and how to break the chain of events that lead to injuries. This will be important as the industry continues to drive itself to be more lean and efficient. “To me, developing an effective business culture is not an initiative,” Gehring says. “An initiative sounds too much like a project that has a start and a stop, and something you can complete. Building a company culture is really a journey. It will change and morph over time.”
Such change is laid squarely on the shoulders of the top senior leaders of the company, according to Gehring, who adds that it then requires support of the other leaders across Rio Tinto Minerals. “You can’t create a culture by sending out an e-mail, or presenting a few PowerPoint slides,” he explains. “You have to be intentional in how you will build that culture by examining, supporting, and changing the system, symbols, and behaviors that create your culture.”