Long before the word sustainable was in widespread usage, there was always a strain of entrepreneurial efficiency in American commerce. Among the best companies to illustrate this was the Ira C. Darling & Company of Chicago. Later to become Darling Ingredients, the company was founded in 1882 at a time when the city was in a period of extreme growth due its famous meatpacking stockyards.
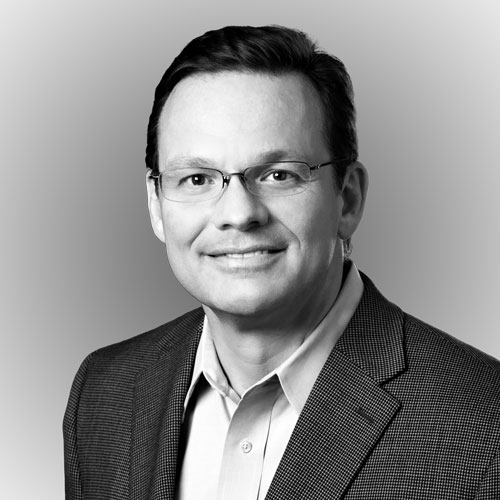
The firm began with the partnership between the Swift meatpacking business and the Darling family as a way to handle the increasing amounts of inedible by-products from the growing beef industry. While the United States’ affection for a meat-focused diet may be well recognized, less understood is the value and diverse use of by-products. The Darling family’s ownership of a fertilizer company in Rhode Island helped them realize the value of using stockyard remnants for agricultural use. As Chicago’s meatpacking businesses were booming, Darling and other renderers were exceptionally industrious at developing markets and methodologies for making use of what was once discarded.
Fast-forward to 2016, and it’s clear that Jeff Holder, Darling Ingredients’ vice president and chief information officer, plays a crucial role in the company’s operations and its 10,000 employees doing business on five continents. The nature of the enterprise—a repurposing of fats, greases, and animal by-products that include gelatins, tallows, meat and bone meal, and more—is the same. But the sourcing of those materials, and Darling’s customers and applications, continues to expand through Holder’s guidance.
“We ask all employees to think and act globally. The path is to empower local people to run their businesses better.”
“We are the original recyclers,” says Holder, speaking from the company’s present-day global headquarters in Irving, Texas. “We’ve been focused on sustainability since our inception.”
Indeed, the firm sources its raw products not only from meatpacking sites in the United States, Canada, South America, Australia, China, Europe, and Japan, but it also collects restaurant fats from food-service facilities in North America. Products are distributed worldwide in the pharmaceutical, food, pet food, feed, technical, fuel, bioenergy, and fertilizer industries.
It’s an operations-intensive business. For instance, imagine the fleets of vehicles and drivers who gather used cooking oil from restaurants, food-service operations, and food-manufacturing facilities throughout North America. It engages logistics on a massive and meaningful scale. About one out of every ten gallons of used cooking oil is converted by Darling Ingredients’ partnership with Valero Energy Corporation (Diamond Green Diesel) to produce renewable diesel, a fuel so similar to petroleum-based diesel that it seamlessly integrates into the existing distribution infrastructure and pipelines.
Or consider Darling’s Rousselot brand, which is the world leader in the production and marketing of gelatin and collagen peptides. These ingredients are sold to the food, pharmaceutical, and cosmetic industries for a variety of applications. The Nature Safe Natural and Organic Fertilizer brand anchors Darling to its origins, providing fertilizers to organic farms, nurseries, golf courses, and turf grass industries. Few if any bone, feather, meat, fish, poultry, or blood components go to waste.
Holder joined the company in 2012, in part to roll out Oracle’s E-Business Suite, an enterprise resource planning system. It’s a complete management system that encompasses financial, human resources, procurement, and production operations of the sprawling company. The initiative is known as Project Edge.
“Project Edge replaces three key legacy systems that were incompatible with our growth strategy,” Holder says. The company performed a number of transformational acquisitions over the last five years. The larger among them include National By-Products and Griffin Industries (both were significant regional animal by-product processors), Terra Renewal Services (repurposing bionutrients from industrial wastewater), Rothsay (a Canadian by-product recycler and biodiesel producer), VION Ingredients (developer and producer of specialty ingredients from animal origin), and Custom Blenders (bakery residual recyclers).
Holder describes the integration process as evolutionary and effective, but already credits Project Edge for surfacing problems that would otherwise impact the company, its operations, and profitability. “These companies, while strategically aligned, maintained different local processes,” Holder says. “Each had their own systems, mostly custom-developed over the last twenty years. But we are striving for whole integration into one Darling Ingredients.”
Project Edge elevates quality and efficiency in this very old industry. Holder’s teams are working on a master data management program within Project Edge that creates a common language between the various acquired companies, their operations, and the varied lines of business with their myriad customers. For example, the raw material functionality is laden with logistics, pricing, inventory, and manufacturing terminology. Data standards and controls allow the billing systems to be coordinated across the board, while simplifying the consolidation and roll-up of financial, payroll, human resources, and indirect procurement data.
Working through moments of volatility in so many customer industries—food, feed, and fuel—requires that Darling’s demand-price dynamics need to be closely managed. “Fat and protein commodity prices can be quite volatile, while the gelatin business, which goes into everything from gelcaps to gummy bears and marshmallows, is typically more stable,” Holder says. “Our global span and diversity provides us with vital intelligence, allowing us to remain agile in the marketplace.” Close monitoring of markets and supplies can also bring opportunities.
Holder emphasizes that uniform systems are not about centralized, top-down control as much as a unified, bottom-up means of decision making. “We’ve doubled in size in the past three years, adding complexity and diverse culture to the company,” he says. “We ask all employees to think and act globally. The path is to empower local people to run their businesses better.”
He describes how idea sharing with acquired companies abroad is already yielding benefits. For example, the European rendering operation provided a new market opportunity for blood by-products in the burgeoning aquaculture segment, where the annual global growth rate is 8.3 percent.
Globalization and sustainability compose core Darling characteristics, while the green nature of what they do is evident everywhere. “Our entire business is about efficient reuse of materials,” Holder says. “It’s at the core of what we do.”